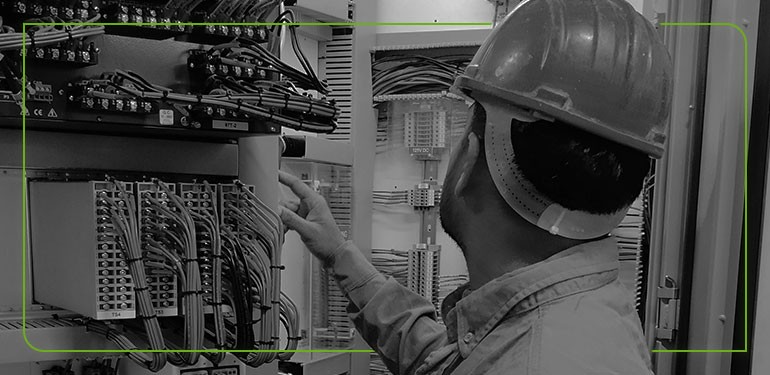
12 Indicadores de Manutenção que Transformam a Gestão Industrial
Em um cenário industrial cada vez mais competitivo, a gestão eficiente da manutenção industrial deixou de ser apenas uma necessidade operacional para se tornar uma vantagem estratégica. Empresas que dominam os indicadores de manutenção industrial conseguem reduzir custos, aumentar a disponibilidade dos equipamentos e, consequentemente, impulsionar a produtividade.
Neste artigo completo, apresentaremos os 12 KPIs mais importantes para sua estratégia de manutenção, com fórmulas práticas, exemplos reais e orientações sobre como implementá-los em sua operação.
O Que São Indicadores de Manutenção e Por Que São Importantes?
Indicadores de manutenção são métricas quantitativas que permitem avaliar o desempenho das atividades de manutenção em uma organização. Eles fornecem dados objetivos sobre a eficiência das operações, condições dos equipamentos e eficácia das estratégias de manutenção implementadas.
O principal objetivo desses indicadores é transformar dados operacionais em informações relevantes para a tomada de decisões, possibilitando identificar áreas problemáticas, priorizar intervenções e otimizar recursos. Com eles, você consegue responder perguntas essenciais como: "Quanto tempo nossos equipamentos operam sem falhas?", "Quão rápido conseguimos resolver problemas?" e "Quanto custam nossas manutenções em relação ao valor produzido?".
Diferença entre KPIs e métricas genéricas
Embora muitas vezes usados como sinônimos, KPIs (Key Performance Indicators) e métricas genéricas possuem diferenças importantes.
Enquanto qualquer dado mensurável pode ser considerado uma métrica, os KPIs são indicadores especificamente selecionados por sua relevância estratégica para os objetivos do negócio.
Por exemplo, o número total de intervenções de manutenção é uma métrica, mas pode não ser um KPI relevante.
Já o MTBF (Tempo Médio Entre Falhas) é um KPI crucial, pois está diretamente relacionado à confiabilidade dos equipamentos e impacta diretamente a produtividade e os resultados financeiros.
Os 12 Principais KPIs de Manutenção Industrial
Você já parou para pensar que o sucesso da sua operação industrial pode estar escondido em alguns números estratégicos? Em nossa experiência com centenas de empresas, percebemos que a diferença entre uma manutenção reativa e cara e uma manutenção estratégica e eficiente está justamente no monitoramento dos indicadores certos.
Não estamos falando de qualquer métrica, mas sim dos 12 KPIs que realmente fazem a diferença no dia a dia da indústria. São esses indicadores que transformarão sua visão sobre manutenção, deixando de ser apenas um centro de custos para se tornar um verdadeiro gerador de valor para o negócio.
Desde o clássico MTBF, que revela a confiabilidade dos seus equipamentos, até a Taxa de Falhas Recorrentes, que expõe problemas crônicos em sua operação, cada indicador que apresentaremos a seguir foi cuidadosamente selecionado com base na relevância prática e no impacto direto nos resultados financeiros.
Vamos explorar:
1. MTBF (Tempo Médio Entre Falhas)
O MTBF é considerado um dos indicadores de manutenção mais importantes em qualquer operação industrial. Ele mede o tempo médio em que um equipamento funciona adequadamente entre uma falha e outra, sendo fundamental para avaliar a confiabilidade dos ativos.
Fórmula: MTBF = Tempo Total Operacional / Número de Falhas
Na prática, você pode calcular o MTBF utilizando a seguinte fórmula:
MTBF = (Tempo total – Tempo perdido) / (Quantidade de paradas)
Por exemplo, se um equipamento operou por 24 horas (tempo total), teve 5 horas de tempo perdido e sofreu 25 paradas não programadas, o cálculo seria:
MTBF = (24 - 5) / 25 = 0,76 horas ou aproximadamente 45 minutos
Quanto maior o valor do MTBF, melhor, pois indica que o equipamento opera por mais tempo sem apresentar falhas.
Erros comuns no cálculo e como evitá-los
Um erro frequente ao calcular o MTBF é incluir o tempo de paradas programadas no tempo total de operação. Lembre-se que o MTBF deve considerar apenas o tempo em que o equipamento estava efetivamente disponível para operar.
Outro equívoco comum é considerar todas as paradas como falhas, quando na verdade apenas as paradas não programadas devem entrar neste cálculo.
Para evitar esses erros, mantenha registros detalhados diferenciando paradas programadas e não programadas, e utilize sistemas automatizados de coleta de dados sempre que possível.
2. MTTR (Tempo Médio para Reparo)
O MTTR é um indicador fundamental que mede a eficiência da sua equipe de manutenção em resolver problemas quando ocorrem falhas. Enquanto o MTBF mostra a frequência das falhas, o MTTR indica quanto tempo leva para corrigi-las.
Fórmula: MTTR = Tempo Total de Parada / Número de Reparos
Na prática, a fórmula pode ser expressa como:
MTTR = (Tempo de parada) / (Quantidade de paradas)
Por exemplo, se um equipamento ficou parado por um total de 3 horas e 45 minutos ao longo de 25 ocorrências de falha, o cálculo seria:
MTTR = 3,75 / 25 = 0,15 horas ou aproximadamente 9 minutos
Ao contrário do MTBF, quanto menor o valor do MTTR, melhor, pois indica que sua equipe resolve problemas mais rapidamente.
Caso real: Como reduzir o MTTR em 30%
Uma indústria de equipamentos agrícolas conseguiu reduzir seu MTTR em 30% implementando três estratégias principais:
-
Criação de um inventário estratégico de peças de reposição para itens críticos
-
Treinamento especializado da equipe de manutenção com foco em diagnóstico rápido
-
Implementação de um sistema digital de gestão que permite acesso imediato a manuais técnicos e histórico de falhas7
Essa redução no MTTR resultou em um aumento significativo na disponibilidade dos equipamentos e, consequentemente, na produtividade da planta.
3. Disponibilidade de Ativos
A disponibilidade é um dos indicadores mais importantes para a gestão de manutenção, pois representa o percentual de tempo em que os equipamentos estão efetivamente disponíveis para produção.
A disponibilidade teórica considera apenas as paradas não programadas, enquanto a disponibilidade operacional inclui também as paradas programadas. Para uma análise completa, é importante monitorar ambas e entender suas diferenças.
Fórmula: Disponibilidade = (MTBF / (MTBF + MTTR)) x 100
Essa fórmula relaciona diretamente os dois indicadores anteriores (MTBF e MTTR). Alternativamente, pode-se calcular:
Disponibilidade = (Tempo total – Tempo perdido) / (Tempo total – Tempo de Parada Programada) x 100
Por exemplo, em um período de 25 horas, com 5 horas e 50 minutos de tempo perdido e 2 horas de paradas programadas, o cálculo seria:
Disponibilidade = (25 - 5,83) / (25 - 2) x 100 = 19,17 / 23 x 100 = 83%
O ideal é buscar uma disponibilidade superior a 90%, embora o valor ideal varie de acordo com o setor e o tipo de equipamento.
4. Confiabilidade de Equipamentos
A confiabilidade indica a probabilidade de um equipamento funcionar adequadamente durante um determinado período sem apresentar falhas. É um indicador essencial para operações críticas onde falhas podem representar grandes riscos.
A manutenção preditiva tem impacto direto na confiabilidade dos equipamentos, pois permite identificar potenciais problemas antes que se transformem em falhas.
Implementar técnicas preditivas como análise de vibrações, termografia e análise de óleo pode aumentar significativamente a confiabilidade dos seus ativos.
Fórmula: Confiabilidade = e^(-Tempo de Operação / MTBF)
Esta fórmula, baseada na distribuição exponencial, calcula a probabilidade de um equipamento continuar funcionando até um determinado momento.
Por exemplo, se um equipamento tem MTBF de 200 horas, a confiabilidade para operar por 100 horas sem falhar seria:
Confiabilidade = e^(-100/200) = e^(-0,5) = 0,607 ou 60,7%
Isso significa que há aproximadamente 61% de chance do equipamento operar por 100 horas sem falhar.
5. Backlog de Manutenção
O backlog representa o acúmulo de trabalho pendente na manutenção, considerando todas as atividades que ainda não foram executadas. Este indicador é fundamental para dimensionar equipes e priorizar atividades.
Um backlog saudável deve estar próximo de 1, o que indica equilíbrio entre a demanda de serviços e a capacidade da equipe. Valores acima de 2 indicam acúmulo excessivo de tarefas e provável sobrecarga da equipe, enquanto valores abaixo de 0,8 podem sugerir ociosidade.
Fórmula: Backlog = Horas Pendentes / Capacidade da Equipe
Para calcular o backlog, some todas as horas estimadas para conclusão das ordens de serviço pendentes e divida pela capacidade da sua equipe no período analisado.
Por exemplo, se você tem 220 horas de trabalho pendente e uma equipe com capacidade para realizar 100 horas de trabalho por semana, seu backlog seria:
Backlog = 220 / 100 = 2,2
Este resultado indica que seriam necessárias 2,2 semanas para concluir todos os serviços pendentes, sem considerar novas demandas que possam surgir.
6. OEE (Eficiência Global de Equipamentos)
O OEE (Overall Equipment Effectiveness) é um indicador composto que mede a eficiência global dos equipamentos considerando três dimensões: disponibilidade, performance e qualidade.
O OEE está diretamente relacionado aos princípios da produção enxuta (Lean Manufacturing), pois ajuda a identificar e eliminar as seis grandes perdas nos modelos de produção: quebras, setups, pequenas paradas, velocidade reduzida, rejeitos e retrabalhos.
Fórmula: OEE = Disponibilidade x Performance x Qualidade
Onde:
-
Disponibilidade = Tempo de operação / Tempo planejado
-
Performance = (Quantidade produzida x Tempo de ciclo ideal) / Tempo de operação
-
Qualidade = Quantidade de produtos conformes / Quantidade total produzida
Por exemplo, com disponibilidade de 85%, performance de 95% e qualidade de 98%, o OEE seria:
OEE = 0,85 x 0,95 x 0,98 = 0,79 ou 79%
Um OEE de classe mundial está em torno de 85%, enquanto a média da indústria geralmente fica entre 60% e 70%.
7. Custos Estratégicos (CMF, CPMV, CMUP)
Os indicadores de custos são fundamentais para avaliar o impacto financeiro das atividades de manutenção e justificar investimentos.
CMF (Custo de Manutenção sobre Faturamento)
Este indicador relaciona os gastos com manutenção ao faturamento da empresa, permitindo avaliar o impacto financeiro das atividades de manutenção no resultado global do negócio.
CPMV (Custo de Manutenção sobre Valor de Reposição)
O CPMV avalia os gastos de manutenção em relação ao valor de reposição do equipamento, ajudando na decisão entre continuar mantendo ou substituir um ativo.
Fórmula: CPMV = (Custo total de manutenção / Valor de reposição) x 100
CMUP (Custo de Manutenção sobre Unidade Produzida)
Este indicador avalia o impacto dos custos de manutenção na precificação do produto, sendo essencial para manter a competitividade.
Fórmula: CMUP = Custo de manutenção / Total de unidades produzidas
Exemplo: CMF ideal para setor automotivo = 3-5%
No setor automotivo, o CMF ideal geralmente varia entre 3% e 5%. Isso significa que, para cada R$ 1 milhão de faturamento, a empresa deve gastar entre R$ 30 mil e R$ 50 mil com manutenção.
Valores acima disso podem indicar processos ineficientes ou equipamentos obsoletos, enquanto valores muito abaixo podem sugerir subinvestimento em manutenção, o que pode comprometer a disponibilidade futura.
8. Cumprimento de Planos Preventivos/Preditivos
Este indicador avalia o nível de aderência da equipe aos planos de manutenção preventiva e preditiva estabelecidos, sendo fundamental para garantir a eficácia dessas estratégias.
Você pode calcular o cumprimento dos planos de manutenção preditiva (MPd) com a seguinte fórmula:
MPd = (Tarefas realizadas do plano de manutenção preditiva / Ações programadas no plano) x 100
O mesmo princípio se aplica à manutenção preventiva (MP):
MP = (Tarefas realizadas do plano de manutenção preventiva / Ações programadas no plano) x 100
O ideal é buscar valores acima de 90%, demonstrando forte aderência aos planos estabelecidos. Valores inferiores podem indicar problemas como falta de recursos, planejamento inadequado ou priorização excessiva de atividades corretivas.
9. Distribuição por Tipo de Manutenção
Este indicador mostra a proporção entre os diferentes tipos de manutenção realizados na empresa (corretiva, preventiva e preditiva), revelando a maturidade da gestão de manutenção.
Uma distribuição considerada saudável em operações industriais maduras seria:
-
Manutenção corretiva: 20% a 30%
-
Manutenção preventiva: 30% a 40%
-
Manutenção preditiva: 40% a 50%
Empresas com mais de 50% de atividades corretivas geralmente enfrentam problemas de disponibilidade e custos elevados.
O objetivo deve ser aumentar gradualmente a proporção de manutenções preditivas, que permitem intervenções mais precisas e menos invasivas.
10. Custo por Hora de Produção
Este indicador relaciona diretamente os custos de manutenção com a eficiência produtiva, sendo particularmente útil para indústrias que operam 24/7.
O custo por hora de produção varia significativamente entre setores. Por exemplo:
-
Indústria alimentícia: R$ 150 a R$ 300 por hora
-
Indústria automotiva: R$ 500 a R$ 2.000 por hora
-
Indústria petroquímica: R$ 5.000 a R$ 15.000 por hora
Comparar seu indicador com o benchmark do setor permite identificar se seus custos estão dentro de padrões aceitáveis ou se há oportunidades de otimização.
11. Fator de Produtividade da Mão de Obra
Este indicador avalia a eficiência da equipe de manutenção, considerando apenas o tempo efetivamente produtivo, também conhecido como "Wrench Time".
Como calcular horas improdutivas:
Para calcular o fator de produtividade, você precisa primeiro identificar as horas improdutivas, que incluem:
-
Tempo de deslocamento
-
Pausas e intervalos
-
Tempo de espera (por peças, ferramentas ou autorização)
-
Tempo administrativo (preenchimento de documentos)
O fator de produtividade é então calculado como:
Fator de Produtividade = (Tempo Total - Tempo Improdutivo) / Tempo Total
Em equipes de manutenção industrial, o fator de produtividade típico varia entre 25% e 35%.
Valores acima de 60% são considerados excelentes e geralmente são alcançados apenas com planejamento rigoroso e processos otimizados.
12. Taxa de Falhas Recorrentes
Este indicador mede a porcentagem de falhas que voltam a ocorrer após uma intervenção de manutenção, revelando a eficácia das análises de causa raiz e das soluções implementadas.
Indicador-chave para análise de causa raiz:
Uma alta taxa de falhas recorrentes (acima de 15%) geralmente indica problemas com:
-
Diagnóstico inadequado da causa raiz
-
Soluções paliativas em vez de definitivas
-
Falta de padronização nos procedimentos de manutenção
-
Treinamento insuficiente da equipe
Para calcular, use a fórmula:
Taxa de Falhas Recorrentes = (Número de falhas recorrentes / Número total de falhas) x 100
O objetivo deve ser manter este indicador abaixo de 5%, demonstrando que as intervenções estão efetivamente resolvendo os problemas em sua origem.
Como Implementar KPIs com o Método SMART
Para que os indicadores de manutenção realmente agreguem valor ao seu negócio, eles devem ser implementados seguindo o método SMART: Específicos, Mensuráveis, Atingíveis, Relevantes e Temporais.
Exemplo de meta: "Reduzir MTTR em 15% nos próximos 6 meses via treinamento de equipe"
-
Específico: Define claramente o indicador (MTTR) e a magnitude da redução (15%)
-
Mensurável: O MTTR pode ser quantificado objetivamente
-
Atingível: Uma redução de 15% é realista considerando o treinamento como estratégia
-
Relevante: Melhorar o MTTR impacta diretamente na disponibilidade dos equipamentos
-
Temporal: Estabelece um prazo claro (6 meses) para alcançar o resultado
Ao definir metas SMART para seus indicadores, você cria um senso de direção claro e facilita o engajamento da equipe em torno de objetivos comuns.
Erros Fatais na Análise de Indicadores (e Como Evitá-los)
Na era dos dados, onde informações são abundantes e sistemas de gestão cada vez mais sofisticados, uma armadilha silenciosa ameaça a eficiência da sua manutenção industrial: a interpretação inadequada de indicadores.
Empresas investem recursos significativos implementando KPIs avançados, mas frequentemente cometem erros fundamentais na análise que comprometem todo o processo decisório.
A gestão eficiente da manutenção industrial vai muito além da simples coleta de números. Quando interpretados corretamente, os indicadores transformam-se em poderosas ferramentas estratégicas que impulsionam a produtividade e reduzem custos operacionais.
Porém, quando mal interpretados, podem levar a decisões equivocadas que afetam negativamente toda a cadeia produtiva.
Nesta seção, abordaremos os três erros mais críticos e frequentes na análise de indicadores de manutenção: o foco excessivo em dados puramente quantitativos, a descontextualização operacional das métricas e a falta de integração entre KPIs de diferentes departamentos.
Compreender esses equívocos e saber como evitá-los é essencial para qualquer gestor que busca excelência operacional e vantagem competitiva no cenário industrial atual. Acompanhe as estratégias práticas que preparamos para transformar sua gestão de indicadores em um verdadeiro diferencial estratégico.
Focar apenas em dados quantitativos
Um erro comum é considerar apenas o valor numérico dos indicadores, sem analisar o contexto qualitativo. Por exemplo, um MTBF alto pode parecer positivo, mas se estiver associado a um regime de operação abaixo da capacidade nominal, pode mascarar problemas potenciais.
Para evitar este erro, sempre analise os indicadores em conjunto e considere fatores contextuais como regime de operação, sazonalidade e condições ambientais.
Ignorar o contexto operacional
Cada equipamento opera em condições específicas que afetam seu desempenho. Comparar indicadores entre equipamentos que operam em contextos diferentes pode levar a conclusões equivocadas.
A solução é segmentar sua análise por família de equipamentos, regime de operação e criticidade, estabelecendo benchmarks específicos para cada contexto.
Não integrar KPIs entre departamentos
Os indicadores de manutenção não existem isoladamente; eles impactam e são impactados por métricas de outros departamentos, como produção, qualidade e finanças. Analisar esses indicadores de forma isolada pode levar a otimizações locais que prejudicam o resultado global.
O ideal é estabelecer um sistema integrado de indicadores que considere as interdependências entre departamentos e alinhe objetivos aparentemente conflitantes, como maximizar a disponibilidade (manutenção) e minimizar custos (finanças).
Conclusão
Os indicadores de manutenção são ferramentas poderosas para transformar a gestão de ativos de um centro de custo para um diferencial competitivo.
Quando implementados corretamente, permitem identificar oportunidades de melhoria, otimizar recursos e aumentar a confiabilidade dos processos industriais.
Neste artigo, apresentamos os 12 KPIs essenciais que toda empresa industrial deveria monitorar, desde os clássicos MTBF e MTTR até indicadores financeiros estratégicos.
A chave para o sucesso está em selecionar os indicadores mais relevantes para seu contexto, implementá-los seguindo o método SMART e utilizar a tecnologia como aliada na gestão industrial para coleta e análise dos dados.
Lembre-se que a jornada de melhoria contínua na manutenção industrial é um processo evolutivo.
Comece pelos indicadores básicos, estabeleça uma linha de base confiável e, gradualmente, expanda seu sistema de medição para incluir métricas mais sofisticadas.
Ao dominar esses 12 indicadores, sua empresa estará no caminho certo para reduzir custos, aumentar a disponibilidade dos ativos e, consequentemente, impulsionar a produtividade e a lucratividade do negócio.
Quer dar o próximo passo na excelência em manutenção? A Aethos Sistemas pode ajudar sua empresa a implementar um ERP para indústria que facilita o monitoramento desses indicadores.
Nossos especialistas estão prontos para desenhar uma solução personalizada para suas necessidades específicas.