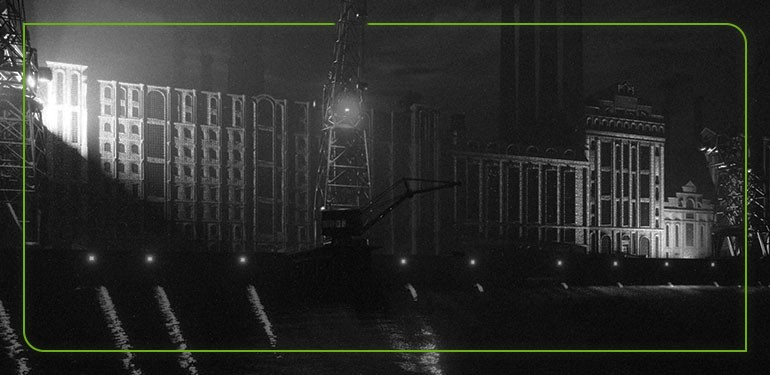
Manutenção Corretiva Planejada: Como Transformar Sua Gestão de Ativos e Reduzir Custos
Você já se perguntou por que algumas empresas conseguem manter suas operações funcionando sem interrupções inesperadas, enquanto outras enfrentam constantemente paradas emergenciais que comprometem a produtividade?
A resposta está na estratégia de manutenção que elas adotam. A manutenção corretiva planejada emerge como uma solução inteligente que combina o melhor de dois mundos: a necessidade de corrigir problemas existentes com a previsibilidade do planejamento estratégico. Esta abordagem tem revolucionado a forma como gestores industriais e empresariais lidam com seus ativos, transformando possíveis crises em oportunidades de otimização.
Ao longo deste artigo, você descobrirá como implementar essa estratégia pode significar a diferença entre uma operação eficiente e uma que constantemente luta contra imprevistos.
O que é manutenção corretiva planejada?
A manutenção corretiva planejada é uma estratégia proativa que envolve a programação antecipada de reparos em equipamentos que já apresentaram algum tipo de falha ou desgaste.
Diferente das abordagens reativas tradicionais, essa metodologia permite que você organize as intervenções de manutenção para causar o menor impacto possível nas suas operações diárias.
Pense na manutenção corretiva planejada como aquele reparo feito de maneira previamente programada, com todos os recursos necessários disponibilizados antes que a falha se torne um problema crítico.
É como quando você percebe que seu carro está fazendo um barulho estranho e agenda uma visita ao mecânico no fim de semana, em vez de esperar que ele pare completamente no meio do trânsito.
A principal distinção entre esses tipos de manutenção corretiva está no momento e na forma como são executados. A manutenção corretiva não planejada acontece quando um determinado sistema ou equipamento apresenta falhas, necessitando de troca ou vistoria emergencial. Ela surge de forma inesperada e geralmente resulta na interrupção temporária do funcionamento do equipamento.
Por outro lado, a manutenção corretiva planejada ocorre quando se detecta uma queda de desempenho em um equipamento, mas as intervenções não são emergenciais e podem ser agendadas.
É indicada para ativos que já estão dando sinais de desgaste, como queda no desempenho, sons ou cheiros estranhos, mas ainda não são graves o suficiente para levar à suspensão das atividades.
Características da manutenção corretiva
A manutenção corretiva, de forma geral, é responsável por restaurar ou corrigir o funcionamento de máquinas e equipamentos. Ela pode ser classificada em diferentes subdivisões, mas sempre tem como objetivo principal devolver ao ativo sua capacidade operacional original.
Você deve estar se perguntando: quando exatamente devo optar pela manutenção corretiva planejada? A resposta está na análise cuidadosa das condições operacionais dos seus equipamentos. Quando identificamos sinais de advertência ou padrões que indicam um problema iminente, temos a oportunidade de planejar a intervenção.
Isso não só ajuda a prevenir falhas antes que se tornem mais graves, mas também melhora o conhecimento geral das condições operacionais dos equipamentos.
A manutenção corretiva planejada utiliza análises de falhas para entender as causas-raízes dos problemas e implementar ações preventivas, visando evitar sua recorrência através de um plano de manutenção estruturado.
Essa abordagem mais organizada e menos disruptiva permite que você se prepare melhor, alocando recursos de maneira eficiente e reduzindo os impactos do tempo de inatividade.
Benefícios da Manutenção Corretiva Planejada
Implementar a manutenção corretiva planejada oferece uma série de vantagens estratégicas que podem transformar completamente a gestão dos seus ativos. Vamos explorar cada um desses benefícios e entender como eles podem impactar positivamente o seu negócio.
Redução significativa de custos operacionais
Um dos principais benefícios da manutenção corretiva planejada é a dramática redução de custos. Quando você programa adequadamente as intervenções, evita as despesas exorbitantes associadas às paradas não programadas.
Imagine a diferença entre agendar a manutenção de um equipamento crítico durante um período de menor demanda versus ter que lidar com uma falha completa no meio de um pico de produção.
As paradas não planejadas são um dos maiores causadores de prejuízos operacionais. Com a manutenção corretiva planejada, você consegue evitar emergências, reduzir o desperdício e planejar gastos de forma muito mais eficaz.
Além disso, você elimina os custos extras com horas extras da equipe de manutenção e peças de reposição adquiridas em caráter emergencial.
Aumento da vida útil dos equipamentos
A manutenção corretiva planejada contribui significativamente para o prolongamento da vida útil dos seus ativos. Quando você intervém no momento certo, evita que falhas menores se agravem, preservando o desempenho e a integridade estrutural dos equipamentos.
É como cuidar da sua saúde: é muito melhor tratar um problema no início do que esperar ele se tornar uma condição grave.
Durante as revisões programadas, você consegue ter uma noção clara de quais peças podem estragar, maximizando não apenas a vida útil da máquina, mas também de seus componentes individuais. Essa abordagem proativa reduz significativamente o desgaste dos equipamentos e permite que você extraia o máximo valor dos seus investimentos.
Previsibilidade operacional e controle de cronograma
Um dos aspectos mais valiosos da manutenção corretiva planejada é a previsibilidade que ela oferece. Quando você programa adequadamente as manutenções, consegue alinhar essas intervenções com sua programação produtiva, reduzindo drasticamente os impactos na operação.
Essa previsibilidade permite que você mantenha um cronograma de produção mais estável e confiável. Seus clientes podem contar com prazos de entrega mais precisos, e você pode gerenciar melhor os recursos humanos e materiais da sua organização.
É a diferença entre navegar com um mapa detalhado versus vagar sem rumo em território desconhecido.
Otimização de recursos e gestão de estoque
A manutenção corretiva planejada permite uma gestão muito mais eficiente dos seus recursos. Com o planejamento adequado, você consegue gerenciar melhor suas equipes, peças de reposição e equipamentos, evitando desperdícios significativos.
Você pode manter um estoque mais enxuto e estratégico, já que sabe com antecedência quando determinadas peças serão necessárias. Isso libera capital de giro que estava imobilizado em estoque desnecessário e reduz os custos de armazenagem.
Além disso, você pode negociar melhores preços com fornecedores quando tem tempo para planejar as compras.
Melhoria da segurança operacional
A segurança é um benefício que não pode ser subestimado. Quando você programa adequadamente as manutenções corretivas, reduz significativamente os riscos de acidentes causados por falhas inesperadas de equipamentos. Equipamentos que operam com problemas conhecidos mas não corrigidos representam riscos tanto para os operadores quanto para o ambiente de trabalho.
A manutenção corretiva planejada permite que você identifique e corrija problemas de segurança de forma controlada, com todos os procedimentos de segurança adequadamente implementados. Isso protege seus colaboradores e reduz a exposição da empresa a responsabilidades legais.
Como fazer a implementação do planejamento de manutenção corretiva?
A implementação eficaz de um programa de manutenção corretiva planejada requer uma abordagem estruturada e sistemática. Vamos explorar um processo passo a passo que você pode adaptar às necessidades específicas da sua organização.
Identificação e classificação de equipamentos críticos
O primeiro passo fundamental é identificar os equipamentos mais críticos para o seu processo. Estes são aqueles cuja falha pode causar interrupções significativas na produção ou impactar severamente a segurança e a qualidade das suas operações.
Para determinar a criticidade dos equipamentos, você pode utilizar métodos como análise de modo e efeito de falha (FMEA), análise de criticidade e matriz de risco.
Essas metodologias ajudam você a classificar os equipamentos com base em fatores cruciais como frequência de uso, severidade das falhas potenciais e possíveis consequências de suas falhas no processo produtivo.
Você deve se perguntar: quais equipamentos, se parassem agora, causariam o maior impacto na minha operação? Estes devem ser priorizados no seu programa de manutenção corretiva planejada.
Crie uma lista hierarquizada que considere não apenas o impacto operacional, mas também aspectos de segurança e custos associados.
Desenvolvimento de um sistema de monitoramento contínuo
Para que a manutenção corretiva planejada seja eficaz, você precisa de um sistema robusto de monitoramento que permita identificar problemas antes que se tornem falhas críticas. Isso envolve a implementação de cronogramas regulares para avaliação de possíveis falhas ou avarias nos equipamentos.
A coleta e análise de dados em tempo real é fundamental nesse processo. Você pode utilizar sensores ou dados de controladoras para monitorar várias condições dos ativos, incluindo vibração, temperatura e fluxo de corrente.
Essas informações devem ser enviadas para um sistema centralizado que permita às equipes de manutenção avaliar regularmente o estado dos ativos e identificar sinais de alerta precoce.
Mantenha um histórico detalhado com avarias e falhas já ocorridas nos equipamentos da sua empresa. Esses dados contribuem significativamente para a criação de inteligência na gestão de manutenção e auxiliam na criação de um calendário de manutenções mais efetivo e preciso.
Planejamento estratégico das intervenções
Uma vez identificados os equipamentos críticos e estabelecido o sistema de monitoramento, o próximo passo é planejar estrategicamente as intervenções de manutenção necessárias.
Isso envolve a elaboração de planos de manutenção específicos para cada equipamento, definindo claramente as atividades a serem realizadas, os recursos necessários e o cronograma de execução.
O planejamento deve considerar cuidadosamente a disponibilidade operacional para minimizar o impacto na produção.
Você precisa garantir que todos os recursos estejam prontamente disponíveis quando necessários, incluindo peças de reposição, ferramentas especializadas e mão de obra qualificada.
Desenvolva procedimentos padronizados para cada tipo de intervenção. Isso inclui a definição de etapas como detecção de falhas, isolamento de falhas, eliminação de falhas e verificação da eliminação de falhas. Cada procedimento deve especificar o tempo adequado para realizar o reparo e os métodos de verificação da eficácia da manutenção.
Utilização de tecnologia e sistemas de gestão
A tecnologia desempenha um papel crucial na implementação eficaz da manutenção corretiva planejada. Sistemas computadorizados de gestão de manutenção como um ERP para indústria são essenciais para programar intervenções, gerenciar ordens de serviço e acompanhar o histórico de manutenção.
Esses sistemas podem criar automaticamente ordens de trabalho com base nos cronogramas estabelecidos, garantindo que as tarefas de manutenção sejam concluídas a tempo e que os recursos sejam corretamente otimizados.
Além disso, eles facilitam a gestão de materiais e inventário, definindo pontos de reabastecimento e automatizando processos de compra.
A análise preditiva é outro aspecto tecnológico importante. Utilizando os dados coletados, sistemas avançados podem prever quando a manutenção deve ser realizada, baseando os cronogramas nas condições reais dos ativos em vez de intervalos predefinidos. Isso melhora significativamente a distribuição dos recursos de manutenção e evita tempo de inatividade inesperado.
Capacitação da equipe e desenvolvimento de competências
A implementação bem-sucedida da manutenção corretiva planejada depende fundamentalmente de uma equipe bem treinada e alinhada com a estratégia.
Você deve garantir que técnicos e gestores estejam adequadamente capacitados para utilizar as ferramentas disponíveis e interpretar corretamente os dados coletados.
Desenvolva programas de treinamento que abordem não apenas os aspectos técnicos da manutenção, mas também a importância do planejamento estratégico e da documentação adequada. Seus colaboradores precisam entender como suas ações individuais contribuem para o sucesso geral do programa.
Estabeleça protocolos claros de comunicação entre as equipes de produção e manutenção. Os operadores são frequentemente os primeiros a identificar sinais de problemas nos equipamentos, e eles precisam saber como e quando reportar essas observações.
Monitoramento de resultados e melhoria contínua
Por fim, estabeleça um sistema robusto de monitoramento de resultados que permita avaliar a eficácia do seu programa de manutenção corretiva planejada. Defina indicadores de manutenção como tempo médio entre falhas, custos de manutenção, disponibilidade de equipamentos e eficiência operacional.
Realize revisões periódicas dos resultados e identifique oportunidades de melhoria. A manutenção corretiva planejada deve ser vista como um processo evolutivo que se aprimora continuamente com base na experiência acumulada e nas mudanças nas condições operacionais.
Você descobrirá que a implementação adequada da manutenção corretiva planejada não apenas reduz custos e melhora a eficiência, mas também cria uma cultura organizacional mais proativa e orientada para resultados. Seus colaboradores passam a pensar estrategicamente sobre a manutenção, e sua organização se torna mais resiliente e preparada para os desafios futuros.
Lembre-se de que o sucesso da manutenção corretiva planejada depende do comprometimento de toda a organização, desde a alta direção até os operadores de chão de fábrica. Quando todos trabalham alinhados com esses objetivos, os resultados são verdadeiramente transformadores para o negócio.