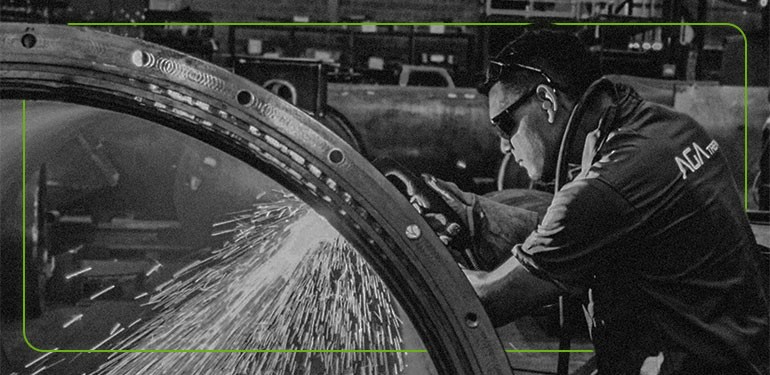
Manutenção Industrial: Como Planejar, Controlar e Alavancar Resultados
Garantir o funcionamento adequado das máquinas e equipamentos tornou-se um fator decisivo para o sucesso empresarial.
A manutenção industrial deixou de ser vista como um mero custo operacional para se transformar em um investimento estratégico que impacta diretamente na produtividade, qualidade e lucratividade do negócio.
Você já parou para pensar quanto uma parada não programada pode custar para sua empresa? Ou como a gestão eficiente da manutenção pode ser um diferencial competitivo?
Neste artigo, vamos explorar todos os aspectos da manutenção industrial, desde conceitos básicos até metodologias avançadas, para que você possa implementar as melhores práticas em sua operação.
O que é Manutenção Industrial?
A manutenção industrial representa um conjunto de ações técnicas e administrativas que têm como objetivo garantir o funcionamento adequado de máquinas e equipamentos em um ambiente fabril.
Segundo a definição da Associação Brasileira de Normas Técnicas (ABNT), na NBR 5462/1994, trata-se de "uma combinação de ações técnicas e administrativas, incluindo as de supervisão, destinadas a manter ou recolocar um item em um estado no qual possa desempenhar uma função requerida".
O conceito de manutenção vai muito além de simplesmente consertar o que quebrou. Ele engloba atividades como inspeções regulares, substituição preventiva de componentes, monitoramento de desempenho, análise de falhas e implementação de melhorias contínuas. Tudo isso para assegurar que os ativos da empresa operem da forma mais eficiente possível, com o mínimo de interrupções não programadas.
A manutenção industrial moderna adota uma abordagem holística, considerando não apenas os aspectos mecânicos, mas também questões relacionadas à segurança dos colaboradores, impacto ambiental, eficiência energética e otimização de recursos. É um campo multidisciplinar que requer conhecimentos de engenharia, gestão e tecnologia da informação.
Para que Serve a Manutenção Industrial?
Você pode estar se perguntando: qual é realmente o objetivo de investir tanto tempo e recursos em manutenção industrial? A resposta é simples: maximizar a disponibilidade dos equipamentos enquanto se minimiza os custos operacionais totais.
A manutenção industrial tem como principais finalidades:
-
Garantir a disponibilidade dos equipamentos: assegurar que as máquinas estejam prontas para operar quando necessário, reduzindo o tempo de inatividade.
-
Prolongar a vida útil dos ativos: através de cuidados regulares, as máquinas e equipamentos podem operar por muito mais tempo antes de precisarem ser substituídos.
-
Aumentar a segurança operacional: equipamentos bem mantidos reduzem significativamente o risco de acidentes no ambiente de trabalho.
-
Reduzir custos operacionais: embora exija investimento, a manutenção adequada evita gastos maiores com quebras inesperadas, peças de reposição emergenciais e perda de produção.
-
Melhorar a qualidade do produto final: máquinas operando em condições ideais tendem a produzir itens com maior conformidade e menor índice de defeitos.
-
Contribuir para a sustentabilidade: equipamentos bem mantidos geralmente consomem menos energia e produzem menos resíduos, alinhando-se às práticas de responsabilidade ambiental.
Segundo estudos do setor, estima-se que em média 4,47% do faturamento bruto das empresas seja destinado a custos com manutenção. Este número evidencia a importância econômica dessas atividades e justifica a necessidade de gerenciá-las de forma estratégica e eficiente.
Principais Tipos de Manutenção Industrial
Existem diversos tipos de manutenção industrial, cada um com características específicas e aplicável em diferentes contextos. Vamos explorar os principais tipos e entender como cada um pode contribuir para sua operação.
Manutenção Preventiva
A manutenção preventiva consiste em ações planejadas realizadas em intervalos predeterminados, baseando-se na vida útil esperada dos componentes. O objetivo principal é reduzir a probabilidade de falhas e prevenir paradas não programadas.
Este tipo de manutenção segue a norma NBR 5462/94 para atender aos aspectos de mantenabilidade e confiabilidade dos equipamentos. As atividades típicas incluem inspeções regulares, lubrificações, ajustes e substituições de componentes antes que apresentem sinais de degradação.
Para implementar uma manutenção preventiva eficaz, é necessário seguir alguns passos importantes:
-
Mapear todos os ativos da operação
-
Determinar a criticidade de cada equipamento
-
Desenvolver planos específicos de manutenção
-
Programar inspeções regulares
-
Implementar um sistema de gestão
-
Treinar adequadamente a equipe
-
Analisar os resultados e fazer ajustes contínuos.
Quando os equipamentos sofrem desgaste natural pelo tempo ou necessitam de cuidados após determinados períodos de funcionamento, a manutenção preventiva se torna a escolha mais adequada.
Manutenção Corretiva
A Manutenção Corretiva entra em cena quando o equipamento já apresentou falha. Ela pode ser dividida em dois tipos:
-
Manutenção Corretiva Não Planejada (Emergencial): ocorre de forma inesperada, sem qualquer supervisão prévia sobre o equipamento. Geralmente resulta em falhas graves que interrompem a produção, exigindo reparos urgentes e mais custosos.
-
Manutenção Corretiva Planejada: baseia-se na identificação prévia de um problema através do acompanhamento das máquinas. Por ser previsível, permite um melhor planejamento e causa menos impacto na produção.
Exemplos comuns de manutenção corretiva incluem reparos em tubulações com vazamento, troca de peças quebradas, conserto de trincas estruturais, reativação de sistemas em curto-circuito e substituição de componentes eletrônicos queimados.
Embora seja impossível eliminar completamente a necessidade de manutenção corretiva, o ideal é que ela represente apenas uma pequena parcela do programa total de manutenção da sua empresa.
Manutenção Preditiva
A manutenção preditiva utiliza técnicas avançadas para monitorar e analisar dados dos equipamentos, identificando potenciais falhas ainda em estágios iniciais. Isso permite que a equipe de manutenção aja antes que ocorra uma falha funcional.
Esta abordagem é extremamente eficiente para prevenir e antecipar problemas nos equipamentos. Segundo a consultoria McKinsey & Company, a manutenção preditiva pode aumentar a disponibilidade de uma linha de produção em até 15% e representar uma economia de até 25% nos custos de manutenção.
O objetivo principal da manutenção preditiva é aumentar a manutenabilidade, disponibilidade e confiabilidade dos equipamentos. Isso é possível graças ao monitoramento contínuo das máquinas em funcionamento, utilizando diversas técnicas como:
-
Análise de vibração
-
Termografia
-
Análise de óleo
-
Ultrassom
-
Monitoramento de parâmetros de processo
Essa abordagem permite identificar a causa raiz dos problemas, antecipando-se às falhas e evitando paradas não programadas.
Manutenção Detectiva e Prescritiva
A manutenção detectiva concentra-se na detecção de falhas ocultas, especialmente em sistemas de proteção e segurança que não são utilizados continuamente. Já a manutenção prescritiva representa o estágio mais avançado das estratégias de manutenção.
A manutenção prescritiva combina monitoramento em tempo real, análise de dados e Inteligência Artificial para não apenas prever falhas, mas também prescrever as melhores ações a serem tomadas. Surgida no contexto da Indústria 4.0, essa abordagem utiliza a digitalização e a conectividade para processar grandes volumes de dados dos equipamentos.
O funcionamento da manutenção prescritiva envolve três etapas principais:
-
Monitoramento: sensores e dispositivos IoT coletam dados em tempo real sobre o desempenho dos equipamentos.
-
Análise: algoritmos de Machine Learning e IA processam esses dados, identificando padrões e anomalias.
-
Prescrição: o sistema gera recomendações específicas sobre as ações a serem tomadas para evitar falhas e otimizar o desempenho.
O objetivo principal desta abordagem é garantir a máxima disponibilidade e confiabilidade dos ativos, reduzindo custos e tempos de inatividade não planejados.
Paradas de Manutenção Planejadas
As paradas de manutenção planejadas são interrupções programadas na produção para realizar serviços de manutenção em grande escala. Diferentemente das paradas forçadas, que ocorrem devido a falhas inesperadas, as paradas planejadas são organizadas com antecedência, minimizando o impacto na produtividade.
Durante estas paradas, é possível realizar:
-
Manutenção preventiva em equipamentos críticos
-
Substituição de componentes desgastados
-
Atualizações de sistemas
-
Limpeza profunda de instalações
-
Testes de segurança e conformidade
O planejamento adequado dessas paradas é essencial para reduzir o tempo de inatividade e maximizar o trabalho realizado. Isso envolve a preparação de peças e ferramentas, alocação de pessoal especializado e coordenação entre diferentes departamentos.
Planejamento e Controle da Manutenção (PCM)
O Planejamento e Controle da Manutenção (PCM) é fundamental para garantir uma gestão eficiente dos recursos e atividades de manutenção. Trata-se de um processo de melhoria contínua que visa controlar e monitorar o funcionamento das máquinas e equipamentos, evitando quebras e paradas no processo produtivo.
O PCM é responsável por planejar o que precisa ser feito, realizar o serviço no momento certo, além de controlar e supervisionar todos os processos de manutenção. Para implementar um PCM eficiente, é importante seguir algumas etapas essenciais:
-
Preparação do cronograma: estabelecer prazos claros para as tarefas de manutenção, orientando as decisões e ajudando a entender o fluxo de cada atividade.
-
Agendamento de paradas: programar antecipadamente os momentos em que os equipamentos ficarão indisponíveis para manutenção, minimizando o impacto na produção.
-
Gestão de ordens de serviço: criar, distribuir e acompanhar as ordens de serviço para garantir que todas as atividades sejam executadas conforme planejado.
-
Controle de estoque de peças: garantir a disponibilidade de componentes e insumos necessários para a realização das manutenções.
-
Análise de indicadores: monitorar KPIs como tempo médio entre falhas (MTBF), tempo médio para reparo (MTTR) e disponibilidade dos equipamentos.
Um PCM bem estruturado permite que a empresa atue de forma proativa, identificando falhas potenciais antes que ocorram, resolvendo rapidamente problemas na operação e otimizando o uso de recursos com eficiência.
Metodologias de Excelência em Manutenção
Para alcançar níveis superiores de eficiência na manutenção industrial, diversas metodologias foram desenvolvidas. Vamos explorar duas das mais importantes.
Lean Manufacturing e 5S
O Lean Manufacturing busca eliminar desperdícios em processos industriais, enquanto o 5S (Seiri, Seiton, Seiso, Seiketsu e Shitsuke) é uma metodologia que visa organizar o ambiente de trabalho de forma eficiente e segura.
Quando aplicados à manutenção industrial, esses conceitos ajudam a:
-
Reduzir o tempo de setup das máquinas
-
Minimizar movimentações desnecessárias durante os serviços
-
Organizar ferramentas e peças de reposição
-
Padronizar procedimentos de manutenção
-
Criar uma cultura de melhoria contínua
A implementação dessas metodologias pode levar a uma redução significativa nos tempos de manutenção e na ocorrência de erros, aumentando a disponibilidade dos equipamentos.
Manutenção Produtiva Total (TPM)
A Manutenção Produtiva Total (TPM, do inglês Total Productive Maintenance) é uma abordagem holística que busca envolver todos os funcionários na manutenção dos equipamentos, do operador ao gerente.
O TPM se baseia em oito pilares fundamentais:
-
Manutenção autônoma
-
Manutenção planejada
-
Melhoria específica
-
Educação e treinamento
-
Manutenção da qualidade
-
Gestão antecipada
-
Segurança, saúde e meio ambiente
-
TPM Office (aplicação dos princípios em áreas administrativas)
Um dos principais objetivos do TPM é alcançar "zero quebras" através do envolvimento de todos os colaboradores na detecção precoce de problemas e na implementação de melhorias contínuas. Empresas que implementam corretamente o TPM frequentemente relatam aumento significativo na eficiência global dos equipamentos (OEE).
Vantagens de Investir em Manutenção Industrial
Investir em um programa de manutenção industrial bem estruturado traz diversos benefícios para sua empresa. Vamos explorar as principais vantagens.
Aumento da Produtividade
Uma gestão eficiente da manutenção contribui diretamente para o aumento da produtividade da sua empresa. Isso ocorre por diversos motivos:
-
Menor tempo de inatividade não programada das máquinas
-
Maior eficiência operacional dos equipamentos
-
Fluxo produtivo mais constante e previsível
-
Redução nos tempos de setup e ajustes
Segundo dados do setor, empresas que implementam programas estruturados de manutenção conseguem aumentar sua produtividade em até 15%, simplesmente pela maior disponibilidade de seus equipamentos.
Redução de Custos
Embora exija investimento inicial, a manutenção industrial bem planejada resulta em significativa economia a médio e longo prazo:
-
Menor gasto com peças de reposição emergenciais
-
Redução nas horas extras para reparos não programados
-
Economia de energia com equipamentos operando em condições ideais
-
Extensão da vida útil das máquinas, postergando investimentos em substituições
É importante ressaltar que o custo de uma falha inesperada pode ser até dez vezes maior que o custo da manutenção preventiva que poderia tê-la evitado. Além disso, há o impacto financeiro indireto das paradas não programadas, como a insatisfação de clientes por atrasos nas entregas.
Maior Confiabilidade dos Equipamentos
A confiabilidade dos equipamentos é essencial para garantir a qualidade e a consistência da produção. Um programa de manutenção eficaz aumenta essa confiabilidade por meio de:
-
Monitoramento constante do desempenho das máquinas
-
Substituição proativa de componentes desgastados
-
Calibração regular de instrumentos
-
Análise e correção das causas raiz de falhas recorrentes
Com maior confiabilidade, sua empresa ganha previsibilidade na produção, facilitando o planejamento e cumprimento de prazos, além de melhorar a reputação junto aos clientes.
Sustentabilidade e Responsabilidade Ambiental
A manutenção industrial também pode contribuir para objetivos de sustentabilidade da sua empresa:
-
Equipamentos bem mantidos consomem menos energia
-
Menor geração de resíduos por falhas ou rejeitos
-
Redução no consumo de recursos naturais pela maior durabilidade dos ativos
-
Prevenção de vazamentos ou emissões que possam causar danos ambientais
Além dos benefícios ambientais diretos, essas práticas também contribuem para a imagem corporativa da empresa e podem facilitar a obtenção de certificações ambientais.
5 Dicas para Implementar uma Gestão de Manutenção Eficiente
Para ajudar sua empresa a desenvolver uma gestão de manutenção industrial de excelência, separei cinco dicas práticas e eficazes:
-
Invista em um sistema de gestão da manutenção (CMMS) ou em um ERP para indústria
Um software especializado permite centralizar informações, automatizar a geração de ordens de serviço, controlar estoques de peças e analisar indicadores de desempenho. Atualmente, existem soluções adaptadas para diferentes portes de empresa e que podem ser acessadas até mesmo via smartphone. -
Capacite continuamente sua equipe
A manutenção moderna exige conhecimentos multidisciplinares. Invista em treinamentos regulares sobre novas tecnologias, técnicas de análise de falhas e metodologias de gestão. Lembre-se que seu maior ativo são as pessoas que executam e planejam as manutenções. -
Estabeleça indicadores claros de desempenho (KPIs)
O que não é medido não pode ser gerenciado. Defina métricas como disponibilidade de equipamentos, tempo médio entre falhas (MTBF), tempo médio para reparo (MTTR) e custo de manutenção por unidade produzida. Analise esses indicadores regularmente e use-os para tomar decisões. -
Adote a manutenção preditiva sempre que viável
As tecnologias de sensoriamento e análise de dados estão cada vez mais acessíveis. Identifique equipamentos críticos e implemente sistemas de monitoramento que permitam detectar falhas incipientes antes que causem paradas. -
Integre operadores ao processo de manutenção
Quem opera diariamente o equipamento geralmente percebe pequenas mudanças que podem indicar problemas futuros. Implemente rotinas de inspeção básica a serem realizadas pelos próprios operadores (manutenção autônoma) e crie canais eficientes para que eles reportem anomalias.
A implementação dessas dicas não precisa ser simultânea. Você pode começar com pequenas melhorias e ir ampliando gradualmente o escopo do seu programa de manutenção industrial. O importante é dar os primeiros passos e criar uma cultura de valorização da manutenção em todos os níveis da empresa.
Lembre-se de que cada indústria tem suas particularidades, e o programa de manutenção ideal para sua empresa deve considerar aspectos como criticidade dos equipamentos, disponibilidade de recursos e objetivos estratégicos do negócio. Consulte especialistas se necessário e adapte as práticas ao seu contexto específico.
A manutenção industrial não deve ser vista apenas como um departamento de suporte, mas sim como um parceiro estratégico que contribui diretamente para os resultados do negócio. Ao implementar as práticas discutidas neste artigo, sua empresa estará mais preparada para enfrentar os desafios da indústria moderna, com maior produtividade, menor custo operacional e produtos de melhor qualidade.
E você, como está a manutenção industrial na sua empresa? Já implementou algumas dessas práticas? Compartilhe sua experiência conosco!